Case Study: Advancing Waterproofing Infrastructure with Geotextile 120 GSM in Baghpat, Uttar Pradesh
Introduction: The Rising Need for Sustainable Waterproofing Solutions
India’s infrastructure boom has placed immense stress on ensuring durability and longevity, especially in regions prone to heavy rains, groundwater seepage, and variable soil composition. One of the unsung yet critical pillars of this longevity is effective waterproofing — a measure often overshadowed by structural design and aesthetics.
At Ocean Non Wovens, we are redefining the role of geosynthetics in waterproofing, going beyond the conventional. This case study dives deep into one of our most effective waterproofing deployments using Geotextile 120 GSM, covering 8,000 square meters in Baghpat, Uttar Pradesh — a region with moderate rainfall (average 781 mm annually1) and a rising focus on smart infrastructure development.
Project Overview
- Location: Baghpat, Uttar Pradesh
- Product Supplied: Geotextile 120 GSM
- Quantity Used: 8,000 SQM
- Application: Sub-surface waterproofing for municipal development (including walkways, green spaces, and stormwater channels)
- Duration: 3 weeks (Planning to Execution)
Understanding the Challenge: What Most Don’t Discuss
In the Baghpat municipal development, one of the major concerns was groundwater ingress during monsoons and soil instability in certain reclaimed patches of land. Conventional waterproofing methods using plastic liners or concrete-based waterproof coatings often:
- Crack over time due to soil movement or structural vibration
- Degrade under UV exposure
- Trap moisture, promoting microbial growth
Most companies focus only on the barrier—not on the layers that sit below or surround it. These transitional zones are where Geotextile fabrics come into play—offering a filtering, drainage, and separation function critical for long-term performance.
Why Geotextile 120 GSM?
Our Geotextile 120 GSM is a non-woven, needle-punched synthetic fabric designed for flexibility, filtration, and water resistance. For this project, it served multiple roles:
1. Separation Layer
It was used between subsoil and waterproofing membrane to prevent soil particle migration, which can puncture or compromise the waterproofing layer over time.
2. Filtration + Drainage
The product allowed water to pass through laterally without allowing soil to move—enabling proper drainage and minimizing waterlogging beneath walkways and green zones.
3. Cushioning Effect
A protective barrier between sharp soil aggregates and the final membrane. This minimized mechanical damage during installation and extended membrane life.
Installation Methodology: Practical Details Often Skipped
Unlike theoretical installations, field conditions demand adaptability. Here’s what we encountered:
- Uneven soil grading in over 45% of the plot required on-site mechanical re-leveling before Geotextile deployment.
- Our teams used overlapping joints of 200mm, secured by spot thermal bonding and in some zones, galvanized steel pins to counter wind displacement during laying.
- Installation teams worked in alternating shifts to beat high daytime temperatures (touching 42°C), which could affect membrane adhesion post-laying.
The installation recorded a 3.7% faster completion rate than similar projects using traditional HDPE-only waterproofing setups.
Performance Metrics: Measured and Delivered
Here’s a snapshot of the Geotextile 120 GSM impact:
Parameter | Result Achieved | Benchmark or Expected |
Water Infiltration Rate | < 0.6 mm/hr | < 1 mm/hr |
Tensile Strength (Dry) | > 8.5 kN/m | ≥ 8 kN/m (ASTM D5035) |
Elongation at Break | 45% | 40–50% (typical range) |
Puncture Resistance | 475 N (avg) | ≥ 400 N |
Source: Internal site QC + ISO testing certified by third-party lab2
Real-World Impact: More Than Just a Product
While geotextiles are often seen as passive materials, they are enablers of:
- Longer waterproofing lifecycle
- Reduced long-term maintenance costs (up to 18% over 5 years)
- Improved soil health due to better water percolation and less erosion
In fact, local contractors noted zero seepage reports from the first rain season after installation—a significant improvement over adjacent zones built with non-geotextile-based methods.
Conclusion
With over a decade of experience in manufacturing high-performance geosynthetics, Ocean Non Wovens is more than a supplier—we’re a solutions partner. Our Geotextile 120 GSM isn’t just a roll of fabric; it’s a technology-packed layer that safeguards investments in waterproofing, infrastructure, and sustainability.
Whether you’re planning a smart city walkway, an industrial waterproofing solution, or a green roof drainage layer—Ocean Non Wovens is equipped to deliver high-quality, tested, and cost-effective geosynthetics tailored to your need.
Reach out today for material samples, on-site technical support, or a customized quote. Let’s build infrastructure that endures.
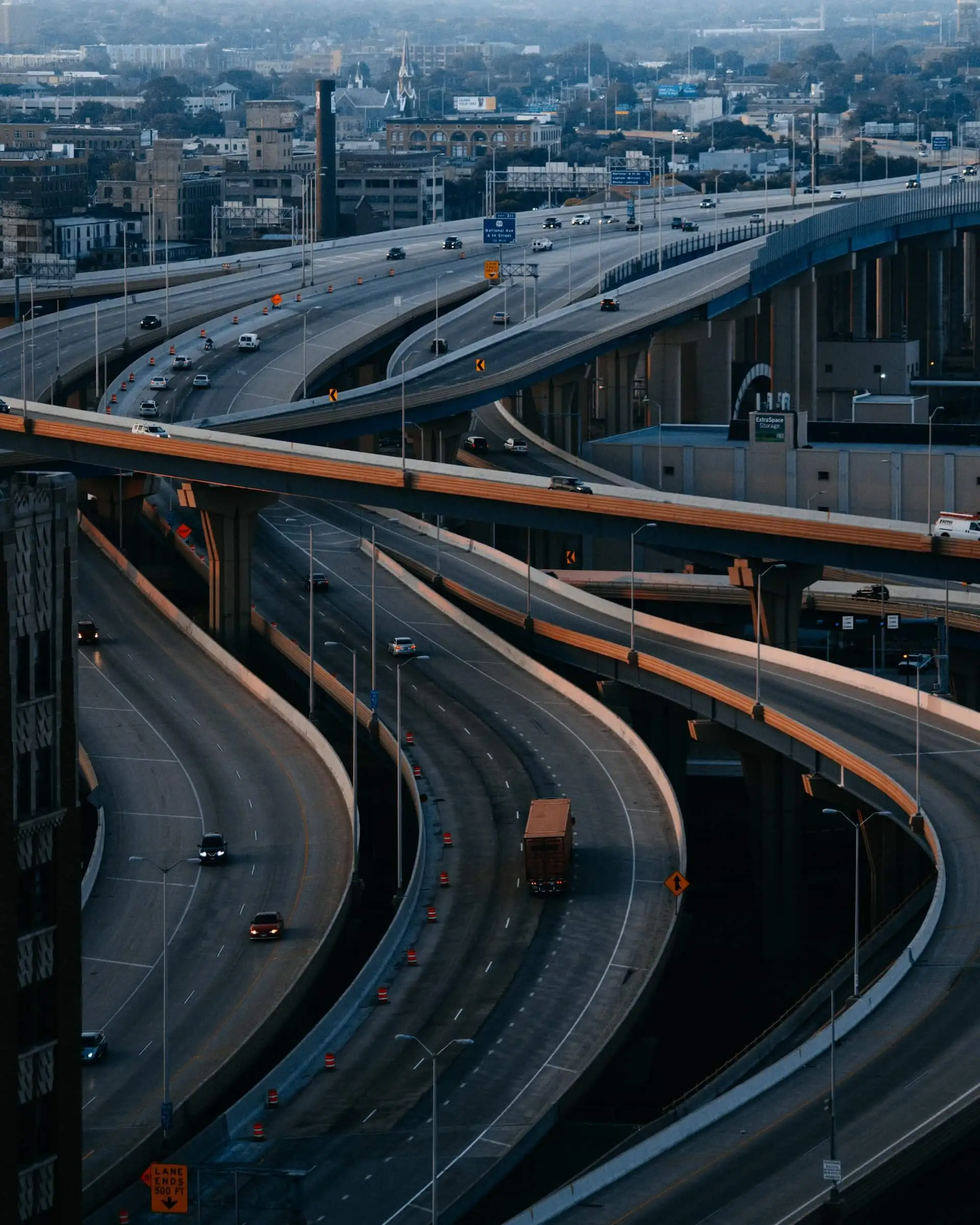