Case Study: Ocean HDPE Liner Installation for Thermal Power Project in Singrauli
Introduction
The thermal power industry is a cornerstone of India’s energy sector, contributing significantly to the nation’s electricity supply. However, with the industry’s rapid growth comes a responsibility to address its environmental impact and resource efficiency. Ocean Non Wovens recently partnered with a thermal power project in Singrauli, Madhya Pradesh, supplying and installing 20,000 square meters of Ocean HDPE Liner-100 Micron. Our high-performance geosynthetic solution was designed to tackle the critical challenges of this project, including seepage control, waste containment, and long-term durability. This case study explores the specifics of our installation process, the unique advantages of using HDPE liners in thermal power projects, and why Ocean Non Wovens’ solutions stand out in the geosynthetics market.
Table of Contents
The Thermal Power Project in Singrauli
Singrauli, often referred to as the “energy capital” of India, is home to several major thermal power plants. These plants play a crucial role in meeting the energy demands of the region and beyond, but they also face unique environmental challenges. Thermal power projects produce by-products like fly ash and bottom ash, which require effective containment and storage. Proper waste containment is crucial to prevent seepage, which can lead to soil and groundwater contamination. The need for a robust, leak-proof containment system in Singrauli was clear, and our Ocean HDPE Liner-100 Micron was the ideal choice for this demanding environment.
Importance of HDPE Liners in Thermal Power Projects
High-Density Polyethylene (HDPE) liners are essential in thermal power plants for various applications, including:
Ash Ponds and Containment Systems:
HDPE liners provide an impermeable layer for ash ponds, preventing leachate from contaminating the surrounding soil and water bodies. Thermal power plants produce massive quantities of ash, necessitating effective containment systems. The HDPE liner’s impermeability plays a crucial role in safeguarding the environment against harmful pollutants contained in the ash.
Water Storage and Sludge Ponds:
HDPE liners are also used in water storage ponds to ensure efficient water management and prevent loss through seepage. Additionally, in sludge ponds, HDPE liners effectively contain sludge and prevent groundwater contamination.
Longevity and Cost-Effectiveness:
HDPE liners are known for their durability and cost-effectiveness, making them a preferred choice for long-term applications. Given the nature of thermal power projects, which have high operational lifespans, HDPE liners ensure that containment systems remain intact and operational with minimal maintenance.
Resistance to Chemicals and UV Exposure:
Thermal power projects often expose containment liners to chemicals, hydrocarbons, and UV radiation. HDPE liners are highly resistant to such conditions, providing an added layer of protection and longevity.
Product Spotlight: Ocean HDPE Liner-100 Micron
Our Ocean HDPE Liner-100 Micron is engineered to meet the specific needs of demanding industrial applications. Here are some of its standout features that made it suitable for the Singrauli thermal power project:
High Tensile Strength and Durability: Ocean HDPE Liners are crafted with high-quality polyethylene, offering excellent tensile strength to withstand the pressures of heavy waste containment. This is especially important in projects like Singrauli, where the liners need to endure large volumes of waste material and varying environmental conditions.
Flexibility and Adaptability: The Ocean HDPE Liner-100 Micron provides a balance between strength and flexibility, allowing it to adapt to ground movements without compromising its integrity. This flexibility is crucial in thermal power projects, where the weight and type of contained material can shift over time.
Chemical Resistance: Designed to be resistant to a range of chemicals, including those found in fly ash and sludge, our HDPE liner ensures that no harmful substances permeate through the liner. This feature is especially valuable for ash ponds, where chemical interactions can be severe.
UV Stability: Given that HDPE liners in thermal projects are often exposed to sunlight for prolonged periods, UV stability is a key requirement. The Ocean HDPE Liner-100 Micron has been tested for UV resistance, ensuring long-lasting protection against environmental factors.
Installation and Implementation in Singrauli
The installation process in Singrauli was planned and executed with precision to ensure maximum liner performance. Here’s an overview of the critical steps involved:
Site Preparation:
Proper site preparation is a fundamental part of any geosynthetic installation. The site was first cleared of debris and leveled to provide a smooth surface for the HDPE liner. Our team ensured that no sharp objects or uneven surfaces could compromise the liner’s integrity.
Liner Deployment and Welding:
The 20,000 Sqm of Ocean HDPE Liner-100 Micron was strategically deployed across the designated containment areas. We used advanced welding techniques to fuse the seams, ensuring a completely leak-proof barrier. Our team utilized extrusion welding for added seam strength, as this method provides superior bonding and durability.
Quality Control and Testing:
Each step of the installation was followed by rigorous quality checks to confirm the liner’s effectiveness. Vacuum testing, air pressure testing, and destructive testing were conducted on selected areas to verify seam integrity and overall liner performance. This comprehensive testing process aligns with industry best practices and standards, ensuring a high-quality installation.
Environmental Compliance:
Compliance with environmental guidelines and regulations was maintained throughout the installation process. The containment system was designed to prevent the leaching of pollutants into the surrounding ecosystem, supporting the power plant’s commitment to environmental responsibility.
Unique Insights and Challenges
While HDPE liners are widely recognized for their durability and chemical resistance, it’s important to note a few nuanced challenges and considerations specific to thermal power projects like Singrauli:
Heat Management:
Thermal power plants generate substantial heat, especially in containment areas. HDPE liners, although resistant, can experience thermal expansion. We accounted for potential expansion during installation by allowing adequate space for the liner to adjust to temperature fluctuations, which ensures minimal wear and tear.
Heavy Equipment Impact:
In industrial settings, HDPE liners can be exposed to heavy machinery. To mitigate the risk of damage, protective layers were added where heavy equipment was frequently operating. This precaution extends the liner’s lifespan and protects against accidental punctures.
Longevity Under Varying Weather Conditions:
Singrauli experiences extreme temperatures and seasonal rains. HDPE liners must withstand these changes without compromising functionality. Ocean HDPE Liners are designed for high UV resistance and flexibility, making them suitable for such climates and ensuring that the liner maintains performance over time.
Project Outcome and Impact
Upon completion, the Singrauli thermal power project was equipped with a robust containment system, effectively managing the waste produced by the plant. Our Ocean HDPE Liner-100 Micron has since played an essential role in containing fly ash and other waste materials, significantly reducing the risk of environmental contamination. The liner’s performance has exceeded expectations, demonstrating excellent durability, leak prevention, and environmental protection.
In a project like this, where containment failures can lead to severe environmental consequences, the quality of the liner is paramount. The installation of our HDPE liner not only supports the operational efficiency of the thermal power plant but also aligns with its environmental goals, setting a standard for responsible waste management in the power generation industry.
Why Choose Ocean Non Wovens for Your Geosynthetic Needs?
Ocean Non Wovens stands out as a leader in geosynthetics, providing solutions that prioritize both performance and environmental sustainability. Our HDPE liners are manufactured with industry-leading materials and precision, ensuring unmatched durability, chemical resistance, and flexibility. We don’t just deliver products; we deliver solutions tailored to each project’s unique needs, backed by a team of experts dedicated to quality and innovation.
If you’re looking to enhance your industrial or environmental project with high-performance geosynthetics, trust Ocean Non Wovens to provide the expertise and products you need. From thermal power plants to landfill sites, we are committed to helping you achieve efficient, eco-friendly, and cost-effective solutions that last. Reach out to us today to learn how we can support your next project with cutting-edge geosynthetics.
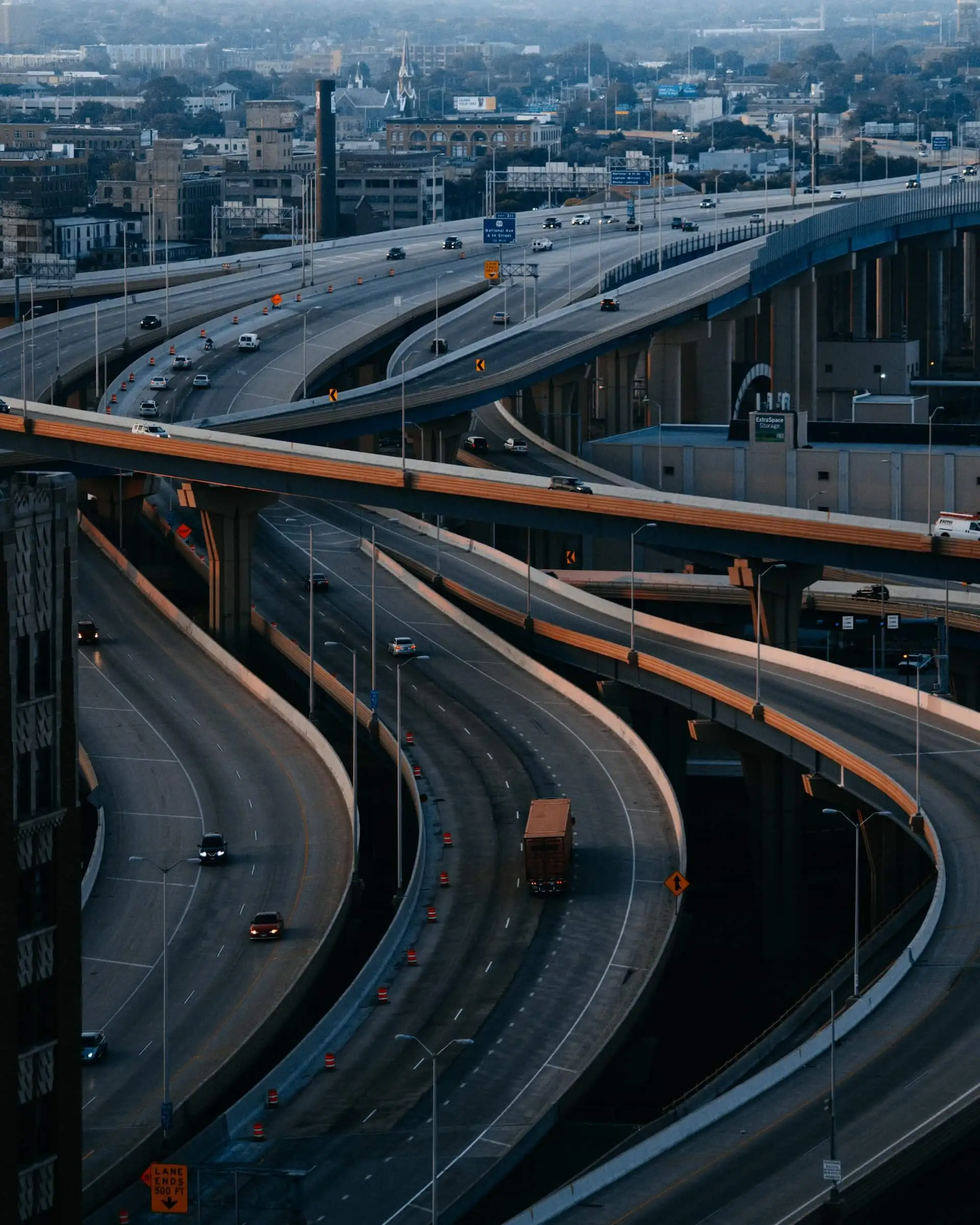