Case Study: Building a Sustainable Oil Pit Storage System in Kharsang, Arunachal Pradesh Using Ocean HDPE Liner – 1500 Micron
In the heart of the remote oil fields of Kharsang, Arunachal Pradesh, the demand for secure, durable, and environmentally responsible oil storage systems is rapidly increasing. To meet these critical needs, Ocean Non Wovens, a trusted geosynthetics manufacturer and supplier, partnered with the project team to deliver a top-tier oil pit containment solution. For this project, we supplied and installed 8400 square meters of Ocean HDPE Liner – 1500 Micron, delivering exceptional performance in one of the most challenging terrains in India.
Table of Contents
Understanding the Importance of Oil Pit Storage
Oil pit storage systems are essential in upstream oil and gas operations. They serve as containment structures for crude oil, drilling mud, production water, and other hydrocarbon-based fluids. These pits not only help in segregating hazardous fluids but also play a crucial role in protecting groundwater and surrounding soil from contamination. With increasing environmental regulations by agencies like the Central Pollution Control Board (CPCB) and Oil Industry Safety Directorate (OISD), the quality and design of these storage systems have become more important than ever.
Why HDPE Liners Are Critical for Oil Pit Storage
High-Density Polyethylene (HDPE) liners are considered the gold standard for oil pit applications due to their chemical resistance, UV stability, and impermeability. Their ability to prevent seepage of oil and chemicals into the earth makes them a sustainable and reliable choice for containment systems. According to a study by the Geosynthetic Research Institute, HDPE liners can reduce leachate migration by up to 99.99%, making them indispensable in oil field projects (GRI Report #38, 2022).
Project Scope in Kharsang, Arunachal Pradesh
The Kharsang oil fields are known for their rough terrain, heavy monsoons, and logistical difficulties. Working in such an environment requires not just a reliable product but also an experienced team that can handle remote deployment and complex ground conditions.
- Location: Kharsang, Arunachal Pradesh
- Purpose: Oil Pit Containment for hydrocarbon fluid segregation
- Product Used: Ocean HDPE Liner – 1500 Micron
- Quantity Supplied: 8400 SQM
- Installation Timeframe: 10 working days
- Sub-grade Preparation: Compacted earth with geotextile underlayer
Technical Overview of Ocean HDPE Liner – 1500 Micron
Ocean HDPE Liner – 1500 Micron is engineered for robust containment applications, especially where high chemical resistance and mechanical strength are non-negotiable.
Key Technical Properties:
Property | Specification |
Thickness | 1.5 mm (1500 Micron) |
Tensile Strength | >28 kN/m (ASTM D6693) |
Puncture Resistance | >600 N (ASTM D4833) |
Chemical Resistance | Excellent for hydrocarbons and acids |
UV Resistance | >90% after 20,000 hours (ASTM G154) |
Lifespan | >20 years under buried conditions |
This HDPE liner complies with GSM and BIS standards, ensuring consistent quality throughout the product lifecycle. Its smooth finish provides ease of installation and superior sealing against earth surfaces.
What Makes Our Oil Pit Installation Unique?
While many companies supply geomembranes, very few talk about the real-world execution challenges—especially in regions like Kharsang. Here’s what set this project apart:
1. Customized Panel Fabrication
To reduce on-site seaming and speed up installation, our team pre-fabricated panels to site-specific dimensions. This minimized material wastage and reduced field welding time by 30%, a critical factor given Kharsang’s unpredictable weather.
2. Thermal Welding Technology
We used double-track thermal fusion welding machines, ensuring joints were 100% leak-proof. Every weld was tested using both air pressure and vacuum box methods to ensure compliance with ASTM D4437.
3. Integrated Drainage System
Unlike most installations, we designed the pit with layered geotextiles beneath the liner to act as a capillary break and provide additional protection against sharp rocks—an often overlooked issue in such terrains.
4. Eco-Conscious Execution
The entire project was completed without harming local water sources or forest cover. We worked in close coordination with the local environmental oversight body to maintain sustainability benchmarks throughout.
Maintenance & Monitoring
We provided the client with a post-installation Quality Assurance & Maintenance Manual, which included:
- Routine inspection schedule (quarterly)
- Leak detection procedures
- Emergency repair protocols
- Expected performance benchmarks over the next 20 years
Such documentation empowers the site team to maintain high containment integrity and avoid environmental penalties under CPCB regulations.
Environmental and Economic Impact
The use of a high-grade geomembrane like the Ocean HDPE Liner – 1500 Micron not only ensures legal compliance but also drastically reduces the risk of environmental liabilities. The cost of remediation after an oil spill can range from ₹5 lakhs to ₹50 lakhs per incident in India (Source: Ministry of Environment, Forest and Climate Change, 2021).
With our containment system in place, the project owner mitigates the risk of groundwater contamination and potential legal action—saving millions in long-term costs.
Why Choose Ocean Non Wovens for Oil Pit Storage Solutions?
At Ocean Non Wovens, we don’t just deliver geosynthetics—we deliver peace of mind. With over a decade of experience in manufacturing and on-site execution, we offer a full-suite solution, from product supply to installation and quality assurance.
Whether you’re working in the oilfields of Assam or the deserts of Rajasthan, our HDPE liners are field-tested and industry-approved. If you’re planning a project that demands environmental safety, chemical resistance, and long-term performance, get in touch with our team for customized geosynthetic solutions that go beyond the surface.
Partner with Ocean Non Wovens—Where Innovation Meets Ground Reality.
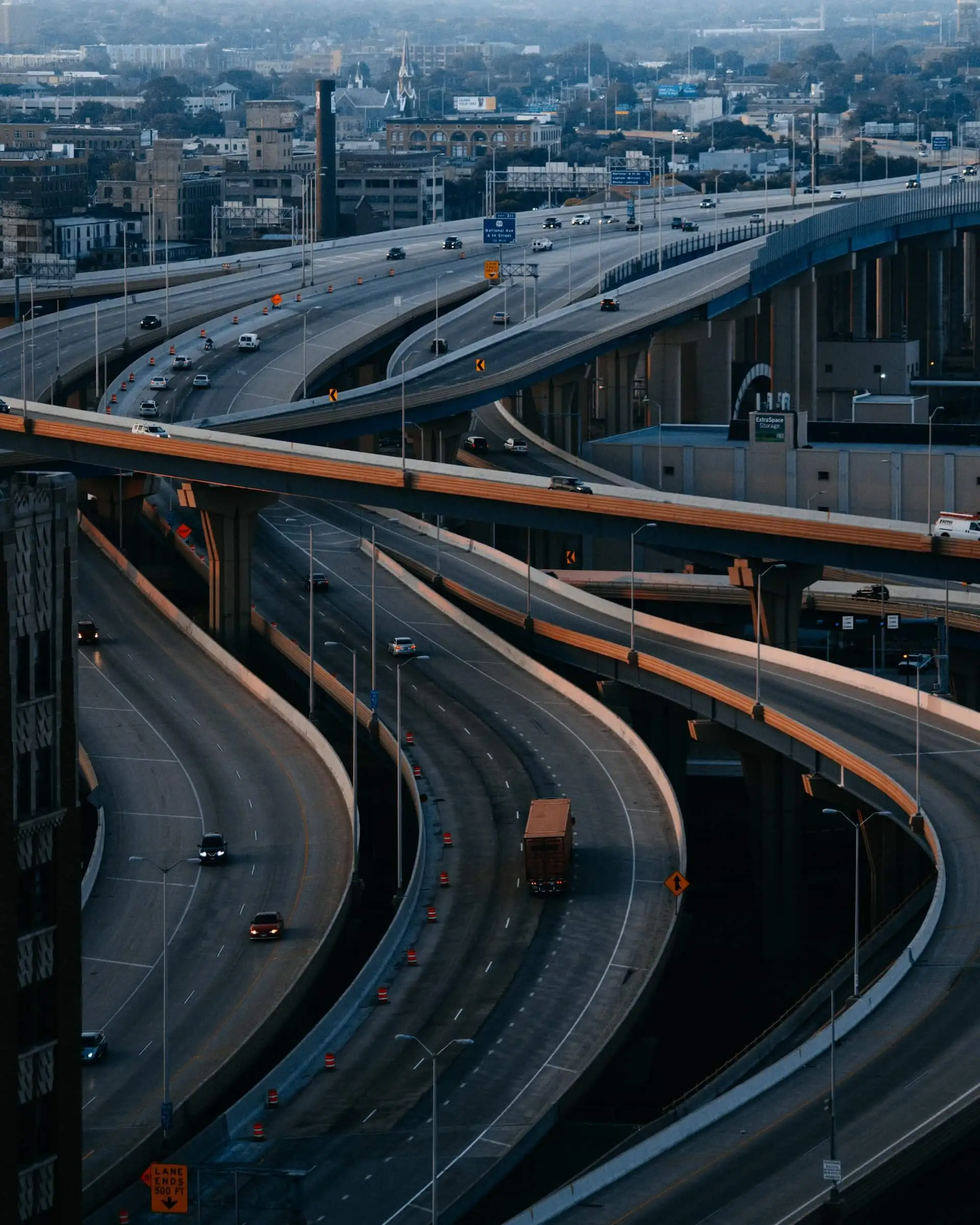