Case Study: Reinforcing Railway Infrastructure in Hotgi, Maharashtra with Ocean Biaxial Geogrid-30kN (80,000 SQM)
Introduction: Railways as the Lifeline of India’s Infrastructure
India has one of the world’s largest railway networks, covering over 68,000 kilometers and transporting nearly 8 billion passengers and over a billion tons of freight annually (Ministry of Railways, 2023). With the increasing axle loads, higher train speeds, and frequent schedules, railway infrastructure today demands not just speed in construction but also longevity, strength, and cost efficiency.
The substructure—particularly the track bed and subgrade—is critical. Weak subsoil or poor drainage can lead to settlement, misalignment, and track failure. That’s why geosynthetics, especially biaxial geogrids, are becoming the material of choice for railway engineers and project authorities.
Geosynthetics in Railway Projects: A Strategic Advancement
Traditionally, railways used thick layers of granular fill and natural aggregates to achieve load distribution. However, in challenging soil conditions or areas with recurring maintenance issues, this approach is costly, time-consuming, and unsustainable.
Biaxial geogrids offer a transformative solution:
- Load Distribution: They help in evenly distributing vertical loads across a wider area, reducing stress on the subgrade.
- Lateral Confinement: Improve track ballast performance by confining aggregate particles and preventing lateral spreading.
- Reduced Settlement: Minimize long-term deformation and track differential settlement.
- Lower Construction Cost: Enable use of marginal fill materials and reduce the thickness of ballast or sub-base.
According to a 2022 report by the Indian Geotechnical Society, the use of geogrids in rail applications can reduce settlement by up to 50% and increase bearing capacity by over 40%.
The Hotgi Railway Project: Technical Overview
Project Overview:
Located in Hotgi, Maharashtra, the project aimed to rehabilitate and reinforce a heavy freight railway corridor that is part of a critical mineral and industrial transportation route in Western India. The stretch had been prone to track misalignment and recurring maintenance due to soft subgrade conditions, especially during monsoons.
Challenge:
- Weak, clayey subgrade with low California Bearing Ratio (CBR) values
- Frequent ballast loss and uneven settlement
- Need for rapid installation without disrupting ongoing traffic
Product Deployed:
Ocean Non Wovens supplied 80,000 SQM of Ocean Biaxial Geogrid-30kN, chosen for its superior tensile strength, optimized aperture geometry, and resistance to UV and mechanical damage.
Technical Properties of Ocean Biaxial Geogrid-30kN:
Property | Specification |
Type | Biaxial Geogrid (Polypropylene) |
Ultimate Tensile Strength (MD) | ≥ 30 kN/m |
Ultimate Tensile Strength (TD) | ≥ 30 kN/m |
Elongation at Max Load | < 12% |
Aperture Size | Optimized for 40–60 mm ballast |
Junction Efficiency | > 90% |
UV Resistance | Excellent (ASTM D4355) |
Chemical Resistance | High (acids, alkalis, organic solvents) |
Execution and Installation
Ocean’s technical team coordinated with project engineers to ensure smooth delivery and timely deployment. The process included:
- Subgrade Preparation: The ground was leveled and compacted to prepare for geogrid installation.
- Geogrid Placement: Rolls were laid with 300 mm overlaps and fastened using polymeric pegs at regular intervals.
- Ballast Placement: Ballast and sub-ballast layers were laid directly over the geogrid without disturbing alignment.
- Vibration Compaction: Mechanically compacted to ensure maximum interlock between geogrid and aggregates.
- Inspection: Conducted post-installation QA/QC tests, including pullout and field plate load tests.
Project Outcomes: What Was Achieved
The use of Ocean Biaxial Geogrid-30kN not only addressed historical ground stability issues but also improved long-term performance and reduced future maintenance needs:
- Reduction in Track Settlement: Preliminary monitoring showed a 42% decrease in settlement compared to non-reinforced sections.
- Improved Bearing Capacity: Subgrade bearing strength improved by an average of 35–40%, allowing for consistent track alignment.
- Accelerated Construction Timeline: Saved nearly 10 working days by minimizing excavation and fill depth.
- Long-Term Cost Savings: Projected to reduce ballast replenishment frequency by 30–40% over a 10-year lifecycle.
- Environmental Benefits: By reducing excavation and natural aggregate usage, the geogrid lowered the project’s carbon footprint.
What Others Don’t Highlight: Lesser Known but Critical Advantages
While strength and durability are often discussed, certain performance aspects of biaxial geogrids are rarely highlighted:
1. Dynamic Load Mitigation
Ocean’s geogrid structure absorbs and redistributes dynamic forces from high-speed trains, reducing vibration propagation into the subgrade—an advantage particularly relevant in freight-heavy corridors like Hotgi.
2. Track Geometry Retention
By minimizing lateral ballast movement, the geogrid helps in retaining track geometry, thus reducing the frequency of tamping operations and line closures.
3. Performance in Wet Conditions
The Hotgi stretch is prone to seasonal waterlogging. Ocean Biaxial Geogrid’s high junction integrity and non-absorbent nature ensure performance does not deteriorate even under submerged or saturated conditions.
4. Reduced Fouling of Ballast
By stabilizing aggregate layers and reducing movement, the geogrid helps prevent fines from migrating upwards, a major cause of ballast fouling.
Why Choose Ocean Non Wovens?
At Ocean Non Wovens, we are not just suppliers—we are solution providers. Our Ocean Biaxial Geogrid-30kN is engineered with high tensile polymers and precision apertures, designed specifically for Indian railway conditions. Manufactured under ISO-certified processes, our geogrids are performance-tested for load retention, field durability, and environmental resistance.
Whether it’s a high-speed passenger route or a freight corridor, Ocean Non Wovens brings deep technical expertise, on-site support, and tailor-made geosynthetics to elevate infrastructure performance.
Planning a rail infrastructure upgrade or facing ground stabilization challenges?
Reach out to Ocean Non Wovens today or explore our geogrid range at www.oceangeosynthetics.com. Let us help you build railways that run smoother, last longer, and perform better—mile after mile.
Frequently Asked Questions (FAQs)
1. What is the purpose of using biaxial geogrids in railway construction?
Biaxial geogrids are used to reinforce the subgrade and ballast layers in railway tracks. They provide lateral confinement to aggregates, distribute train loads more evenly, reduce settlement, and extend the lifespan of the railway track. This is especially crucial in areas with weak or moisture-sensitive soils.
2. How does Ocean Biaxial Geogrid-30kN improve track stability?
Ocean Biaxial Geogrid-30kN offers a balanced tensile strength of 30kN/m in both directions, which enhances the load-bearing capacity of the subgrade. It reduces ballast movement, controls differential settlement, and helps retain track geometry over time, resulting in lower maintenance needs.
3. Is geogrid installation disruptive to ongoing railway operations?
Not at all. One of the key advantages of using biaxial geogrids is their ease and speed of installation. In the Hotgi project, for example, the use of geogrids reduced construction time by approximately 10 days without disrupting railway operations, thanks to minimal excavation and quick deployment.
4. Can biaxial geogrids perform well in waterlogged or monsoon-prone regions?
Yes. Ocean Biaxial Geogrid-30kN is made from high-modulus polypropylene and has excellent resistance to water, UV exposure, and chemical degradation. It maintains performance under submerged conditions, making it ideal for monsoon-affected areas like Maharashtra.
5. How do I determine the right geogrid specification for my railway or infrastructure project?
Choosing the right geogrid depends on multiple factors—soil type, expected loads, traffic frequency, and project goals. At Ocean Non Wovens, our team offers free technical consultations and site-specific design support to help you select the most suitable geosynthetics solution.
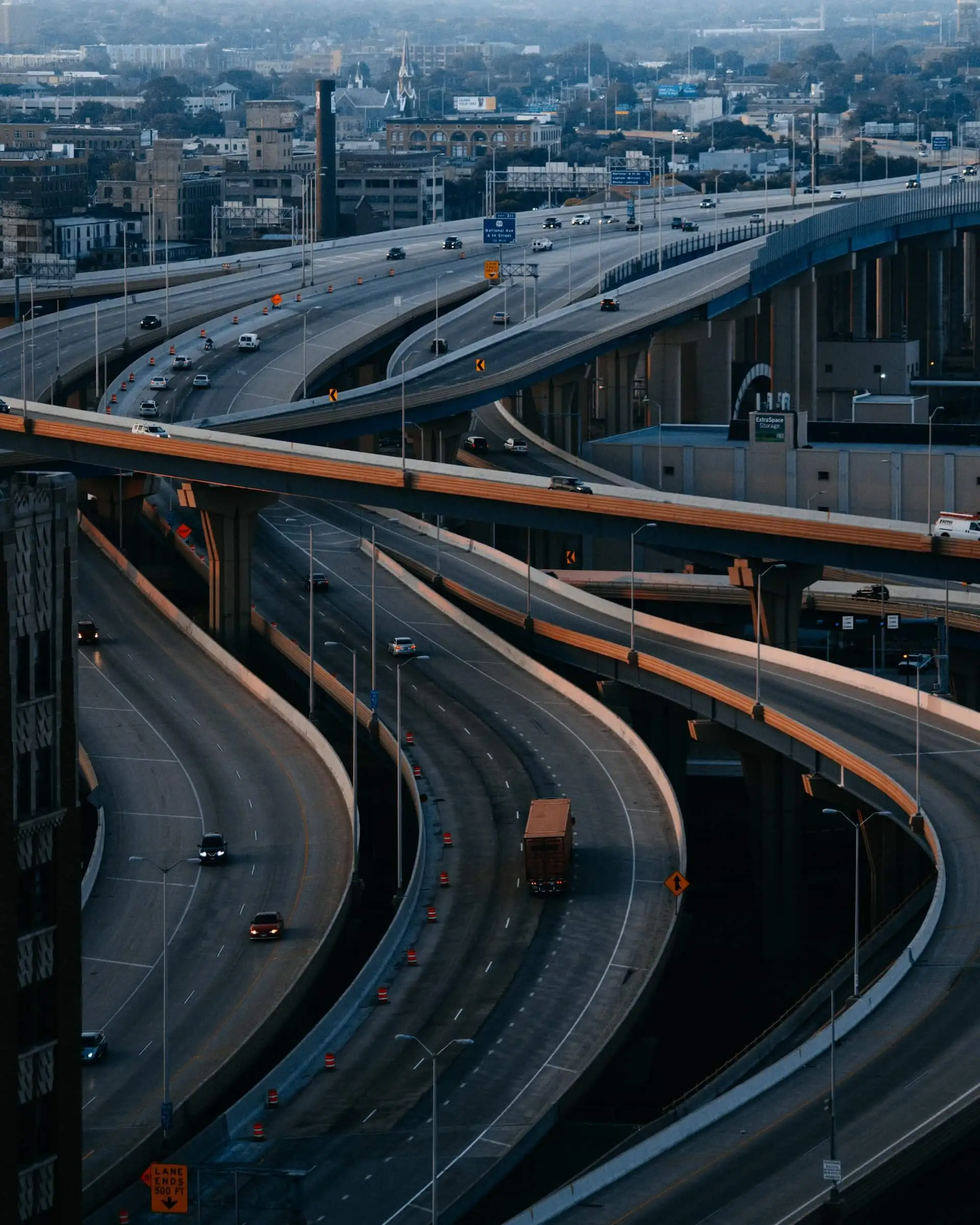