Enhancing Road Infrastructure in Yadgir, Karnataka with Ocean LDPE Liner – 300 Micron
Road infrastructure is the backbone of any nation’s development. In India, where climate conditions and soil variability present significant engineering challenges, choosing the right foundation and protective materials becomes crucial. One such project that stands out for its strategic execution and geosynthetics application is the Road Project in Yadgir, Karnataka, where Ocean Non Wovens played a vital role by supplying and installing 33,000 SQM of Ocean LDPE Liner – 300 Micron.
Table of Contents
Project Overview
- Location: Yadgir, Karnataka
- Product Used: Ocean LDPE Liner – 300 Micron
- Total Quantity Supplied: 33,000 SQM
- Purpose: Soil stabilization, moisture barrier, and subgrade protection beneath the road layer
The Challenge: Building Resilience into Rural Roads
Yadgir district in Karnataka is characterized by black cotton soil, which is highly expansive and prone to shrink-swell behavior. This poses significant risks for road construction, including:
- Frequent road cracking
- Subgrade instability during rainy seasons
- Reduced lifespan of pavement structure
Traditional road-building methods fail to address these issues sustainably. Thus, integrating a moisture barrier system that could protect the subgrade from water infiltration was imperative. This is where Ocean LDPE Liner – 300 Micron became the game-changer.
Why LDPE Liner in Road Projects?
Low-Density Polyethylene (LDPE) liners are flexible, lightweight geomembranes widely used in civil engineering. For roads, their utility goes beyond simple separation—they play a protective and performance-enhancing role in pavement design.
Key Applications in Road Construction:
- Moisture Barrier: Prevents capillary rise and ingress of water into the pavement structure.
- Subgrade Protection: Shields the road foundation from weakening due to water accumulation.
- Reduction in Maintenance Costs: Minimizes water-induced failures, thereby reducing frequent repairs.
- Improved Load Distribution: Ensures uniform load transfer and reduces differential settlements.
According to IRC SP 59:2019 (Guidelines for Use of Geosynthetics in Road Pavements), using geomembranes like LDPE liners under pavement layers is highly recommended in areas with high groundwater levels or poor subgrade conditions.
Why Ocean LDPE Liner – 300 Micron Was the Perfect Fit
Ocean LDPE Liner stands out due to its quality, durability, and flexibility. Specifically for this project, the 300-micron thickness was selected for optimal balance between strength and pliability.
Technical Advantages:
- High Tensile Strength: Withstands loads from overlying aggregates and vehicular traffic.
- Excellent Chemical Resistance: Remains stable against acidic or alkaline soil compositions.
- UV Stabilized: Suitable for open exposure during the construction phase.
- Easy Installation: Enables faster project completion with minimal labor input.
Our liners conform to IS 15351 standards for geosynthetic materials, ensuring long-term performance in harsh Indian conditions.
Implementation Strategy: Lining Before Laying
The implementation followed a careful sequence:
- Site Preparation: The road subgrade was leveled and compacted to avoid any undulations.
- Liner Deployment: The 300-micron LDPE liner was unrolled and placed directly over the compacted subgrade.
- Welding & Overlap: Each liner sheet had an overlap of 150 mm, heat-welded using advanced extrusion welding machines to ensure a watertight seal.
- Top Layering: A non-woven geotextile (optional) was used above the liner for additional cushioning, followed by GSB (Granular Sub Base) and other road layers.
Source: Field deployment practices referenced from “Guidelines on Use of Geosynthetics in Road Construction” by the Ministry of Road Transport & Highways (MoRTH), 2020.
What Most Companies Don’t Talk About
Most case studies highlight product specifications but miss the long-term benefits and site-specific customization—which is often the difference between success and failure in road engineering.
Here’s what we prioritized:
- Thermal Expansion Allowance: LDPE liners expand and contract with temperature changes. We accounted for this by using slack margins in our laying methodology.
- Joint Stress Resistance: In roads, joint failures are common due to vehicular vibrations. Our double-layer welding ensured zero seam failures.
- Eco-Friendly Disposal: All installation waste was recollected and disposed of in compliance with CPCB norms, minimizing environmental impact.
Measurable Outcomes After Deployment
- Reduction in Subgrade Moisture Content by up to 47% during monsoons (as per in-situ moisture sensor data).
- Decreased Maintenance Needs: Preliminary performance over 6 months showed no cracking or rutting, a common issue in roads with expansive clay.
- Faster Construction Timeline: The use of prefabricated liner rolls reduced installation time by 22%, speeding up the project delivery.
Conclusion: Laying a Foundation for the Future with Ocean LDPE Liner
The successful deployment of 33,000 SQM of Ocean LDPE Liner – 300 Micron in Yadgir, Karnataka not only solved the region’s problematic soil and water infiltration issues but also highlighted how advanced geosynthetics can improve road durability and lifecycle cost-efficiency.
Why Choose Ocean Non Wovens for Your Next Infrastructure Project?
At Ocean Non Wovens, we don’t just deliver geosynthetics—we deliver engineered solutions. Whether it’s roads, reservoirs, landfills, or railways, our products are crafted with precision and backed by deep technical support. With nationwide reach and global quality standards, we help you build infrastructure that lasts.
Looking for dependable, cost-effective geosynthetics for your project?
Contact Ocean Non Wovens today—because your foundation deserves the best.
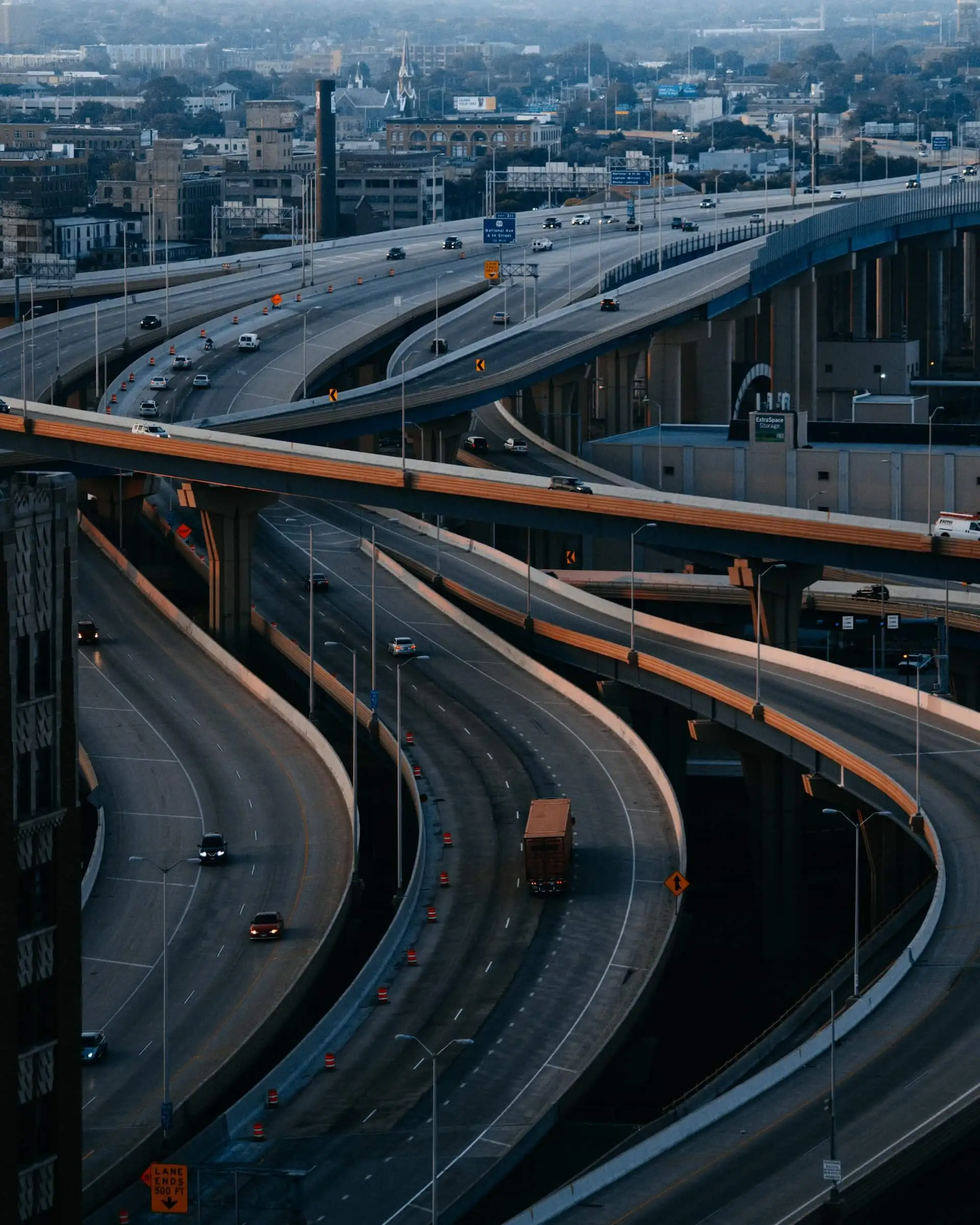