Case Study: Enhancing Runway Performance at Bangalore Airport with 63,602 SQM of Non-Woven Geotextile (200 GSM)
Introduction
Airports do much more than shuffle people around; they are long-lasting, backbone assets designed to keep every single flight safe. With Indias sky traffic on course to be the world’s third largest by 2026, the push for more durable and smarter runways and terminals grows louder daily, says IATA. Quietly supporting this expansion is a simple but essential material that keeps showing its value: non-woven geotextiles. Ocean Non Wovens recently played its part for Runway Upgrade at BLR Airport(Kempegowda International Airport in Bangalore), a busy gateway already welcoming over 33 million travelers every year. For the runways and taxiways, engineers specified our 200 GSM sheet to add strength and stability to the underlying layers.
Why Geosynthetics in Airport Infrastructure?
Airport pavements undergo intense stress from heavy aircraft loads, repeated takeoffs and landings, and high surface friction demands. Traditionally, thick layers of granular materials were used to ensure subgrade stability. However, such methods are both cost-intensive and unsustainable.
That’s where non-woven geotextiles shine:
- Separation: By interposing a porous mat between gravel and soil, they stop the two from mixing and losing strength over years of traffic.
- Filtration: The fabric lets water drain freely while trapping tiny soil grains, lowering pore pressure that would otherwise lift the runway from below.
- Drainage: Aids vertical and horizontal water movement, keeping the ground under the pavement from becoming waterlogged.
- Reinforcement: Spreads load over a wider area, helping to cut rutting and settlement.
A report from the International Geosynthetics Society IGS finds that adding geosynthetics to airport work can thin the base by 20-30, trim costs by 10-15, and add years to pavement life.
The Bangalore Airport Project Technical Overview.
Scope
The job included new taxiways and the strengthening of runway subgrade layers at Bangalore International Airport. Because of its size and critical role, the site needed materials engineered to perform reliably under heavy stress.
Product Supplied
Ocean Non Wovens supplied 63,602 SQM of Non-Woven Geotextile Fabric (200 GSM). Our product was selected after careful consideration of factors such as tensile strength, puncture resistance, permeability, and durability under cyclic loading.
Technical Specifications of the Geotextile Used:
Property | Value |
Type | Needle-punched Non-Woven |
GSM | 200 GSM |
Grab Tensile Strength | ≥ 400 N |
Elongation at Break | ≥ 50% |
CBR Puncture Resistance | ≥ 1200 N |
Permeability | 10⁻³ to 10⁻⁴ cm/sec |
UV Resistance | > 70% strength retention @500hrs |
Installation Process:
Installation was carried out under strict supervision, considering alignment, overlap, and anchorage to ensure performance:
- Subgrade Preparation: The soil was compacted and graded.
- Geotextile Laying: Rolls of non-woven fabric were unrolled, maintaining an overlap of 300 mm between sheets.
- Aggregate Layering: Granular sub-base (GSB) material was placed directly above the geotextile.
- Quality Assurance: On-site pullout tests and puncture resistance checks were conducted at random intervals.
Results and Benefits Achieved
The use of our 200 GSM non-woven geotextile offered multiple performance and economic benefits:
- Improved Load-Bearing Capacity: The geotextile reinforced the subgrade, enabling it to bear aircraft loads more uniformly and reduce differential settlement.
- Cost Savings: Reduction in granular fill thickness led to material and transportation cost savings, estimated at around 8–10%.
- Faster Construction: Installation speed improved as the material was easy to deploy even over undulated surfaces.
- Enhanced Drainage: The geotextile helped drain excess water during monsoons, reducing maintenance downtime.
- Sustainability: Geotextile use reduced the carbon footprint by cutting down on excavation and fill operations.
What Most Don’t Talk About: Subtle Impacts That Matter
While many talk about geotextile performance in terms of strength and drainage, the lesser-discussed impacts include:
- Long-Term Reduction in FOD (Foreign Object Debris): Better subgrade integrity means fewer surface cracks and dislodged materials—key in preventing FOD damage to aircraft.
- Prevention of Pumping Phenomena: Repeated wheel loads on saturated soils often lead to fines being pumped to the surface. Our non-woven geotextile acted as a barrier and filtration layer to mitigate this.
- Thermal Insulation Effect: Though minimal, the fiber matrix of the fabric helped modulate soil temperature changes slightly, reducing frost susceptibility during cooler months.
These are the silent contributors to increased operational safety and reduced lifecycle costs of airport pavements—insights not always shared in conventional geosynthetics use cases.
Why Ocean Non Wovens?
At Ocean Non Wovens, we understand that every square meter of geotextile fabric plays a critical role in infrastructure projects—especially those as vital as airport construction. Our products are manufactured using state-of-the-art needle punching technology with strict adherence to ASTM and BIS standards.
We don’t just supply materials—we provide technical support, on-site supervision, and custom specifications to meet your unique project needs.
Whether it’s an airport runway, a railway embankment, or a highway foundation, Ocean Non Wovens is your trusted partner for reliable and innovative geosynthetics.
Want to ensure the durability and performance of your next infrastructure project?
Explore our full range of non-woven and woven geotextiles at oceangeosynthetics.com or contact us to discuss how we can support your next airport or civil engineering venture with precision-engineered geosynthetic solutions.
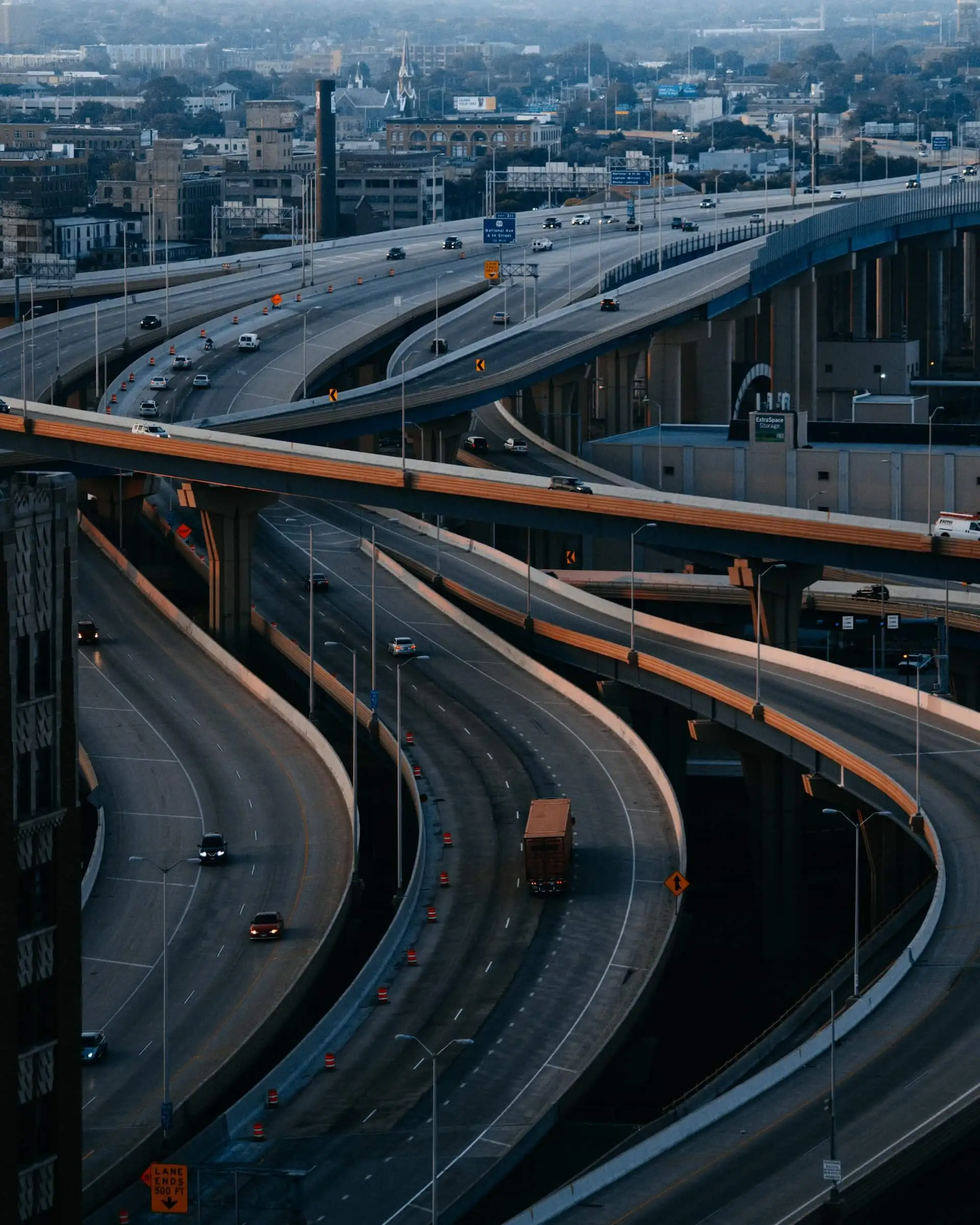