Geotextile Dewatering Bags Used for Desludging Wastewater Ponds
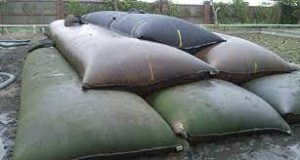
When wastewater treatment ponds reach their quantity, they can either develop new or empty extant facilities. These ponds must be dislodged to make available more space for waste. Though mandatory, strict environmental regulations in wastewater treatment can convolute functional upgrades to a facility.
Here, geotextile dewatering bags gives an efficient, cost-effective approach for desludging works. They can work within a limited footprint and effectively contain the material that requires be removing and disposing of with less environmental impact.
Table of Contents
Geotextile Dewatering Bags in South African Wastewater
The ultimate objective of wastewater treatment is to convert unsuitable fluid into an effluent that is safe to return to the environment. Solid particles (sludge) are divided from the wastewater and delivered to safe disposal sites or included in a tailings storage facility.
Cost-effective and efficient solids separation remains an objection to wastewater tailings facilities around the world.
South Africa serves as a solid example for tackling common wastewater treatment issues with the utilization of geotextile dewatering bags. Here, diverse wastewater treatment sites were identified as having reached their highest storage capacity. Excess sludge accumulation was a major aspect.
Sludge Removal and Dewatering Choice
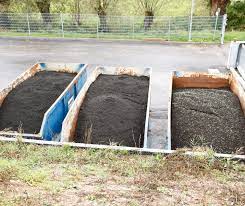
Dredging is the most named form of sludge removal followed by other methods including mechanical removal from a tailings dam. The sludge is eliminated, dried, and delivered to a landfill or land application at ease. However, dredging can be extremely tough, time-consuming, and expensive. Dredging can as well as damage a lining system, this can accord the structural integrity of the sludge pond and lead to seepage.
For the South African projects explained here, limited account and time-sensitive operational upgrade windows for desludging the wastewater ponds pressured the project teams to find substitute methods. On-site geotextile dewatering bags were found to be a more cost-effective and tiny footprint solution.
Conspiring with Dewatering Bags
For the projects here, a dewatering area was coated with a 1-mm-thick Geomembrane to prevent local erosion and to compile all the effluent that would be released from the geo bags during the dewatering process. The effluent would then be carried back into the dam or taken for the next treatment.
The geotextile dewatering bags created out of UV-stabilized woven polypropylene (PP) geotextile material with high-strength seams were utilized to capture the dredged sludge whilst minimizing water loss. The seam strength of a geotextile dewatering bag is important for durability in service and withstanding the stresses associated with pumping the material at high pressures.
The thread utilized to stitch the bags in this project series offered a higher breaking strength than the geotextile itself, hence providing sufficient tensile strength to the bags.
One of the main sources of efficiency in the use of geotextile dewatering bags rests in how they let water flow through the geotextile pores while filtering out the solids, which are interred inside the bag. Even solids smaller than the aperture openings in the fabric are interred, as a filter cake builds up during the dewatering process but does not completely block water flow. This creates an equivalent two-stage filter with filtration efficiencies above 98% for fine-grained material filtered through woven, high-vigor geotextile dewatering geobags.
To shelter the pipe connections, two inlets per bag of standard size 200 mm were accepted. These inlets accommodated pipe amounts up to 200 mm in diameter. When the filling processes were finished, the pipes were detached and the inlets were tied off.
The pumping estimate was kept below 40 m³/h. A manifold was present to break the flow and reduce the inlet speed in the event a pump outstrips the designed rate. The pumping rate did not impact the flow-through rate of the geotextile dewatering bags, due to the aperture size of the geotextile controlling the outflow.
On the account of disposal, the final disposal site for the dewatering geotextile bags should be as near to the generation area as possible to minimize transportation costs. The retained solids can be safely biased off or perhaps reused advantageously, like in fertilizer. The geobags themselves must be part of the responsibility, as they are not recyclable
In the collection of a disposal site, one must:
- Assure that the disposal site is not located in a sensitive area where disposal is not permissible
- Make sure that the sludge disposal site is located as far as possible from the area where the end effluent is discharged to limit possible contamination of the final effluent, as well as to limit the possible addition of contamination to the water resource
- Allow for the maximum buffer areas, more than 400 m from surface water
- Deal with the slope of the disposal site to minimize run-off, erosion, and ponding.
- Make sure that the disposal site is not within the 1:100-year flood line.
- No flocculants were mandatory, as the utilization of geo bags enabled the material to dewater quickly enough by gravity only, yet reducing project costs.
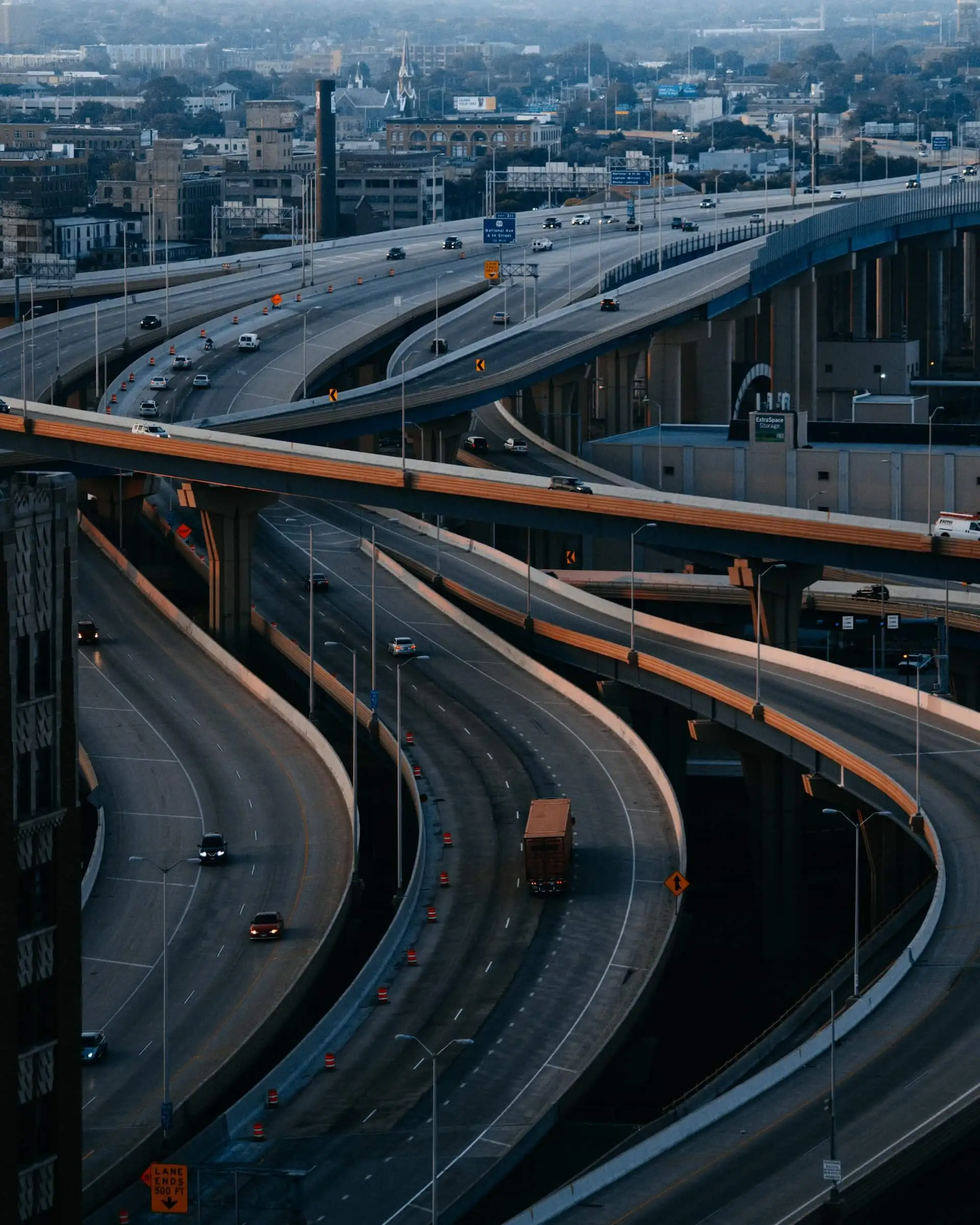