Case Study: Crawfish Hatchery Building Project in Bhutan
Crawfish hatcheries are essential for sustaining aquatic ecosystems and promoting sustainable seafood industries. Ocean Non Wovens, a leading manufacturer and supplier of geosynthetics, contributed significantly to the construction of a Crawfish Hatchery in Bhutan. This project marked another successful venture, where our team supplied and installed 7500 square meters of Ocean HDPE – 750 Micron, a crucial material in modern aquaculture infrastructure. In this case study, we will explore the materials used, the installation process, and the impact on the hatchery’s operations.
The Importance of Geosynthetics in Crawfish Hatchery Construction
Building a crawfish hatchery demands meticulous planning and durable materials to create an environment conducive to breeding and growth. High-quality geosynthetics play a pivotal role in ensuring optimal water containment and preventing leaks, which are critical in aquaculture systems. The liner acts as a barrier that separates the water from the surrounding soil, protecting the water from contamination and ensuring a stable habitat for crawfish.
Ocean HDPE – 750 Micron is a particularly effective solution for these projects. It is designed to withstand harsh environmental conditions, resist punctures, and provide long-term durability, making it an ideal choice for crawfish hatcheries. The material’s unique properties help to:
– Prevent water loss through seepage, thereby maintaining the water levels critical for hatchery operations.
– Provide a barrier against soil contaminants and external pollutants that can affect the health of the hatchery ecosystem.
– Offer a flexible yet durable solution that adapts to the natural ground movement without compromising its integrity.
Why Ocean HDPE – 750 Micron?
Ocean HDPE (High-Density Polyethylene) – 750 Micron is a high-performance liner that boasts several advantages over traditional materials. It was chosen for the Crawfish Hatchery Building Project due to its:
1. Durability and Strength: Ocean HDPE – 750 Micron is resistant to punctures and tears, which are common issues in aquaculture systems where sharp objects or rocks can damage the liner. Its strength ensures that the liner remains intact even under pressure from water and soil movement.
2. Chemical Resistance: The liner is designed to be chemically inert, providing resistance to various organic and inorganic substances that might otherwise degrade other materials over time. This feature is crucial in hatcheries, where water quality must be maintained at optimal levels to support the delicate lifecycle of crawfish.
3. UV Stability: With the hatchery located in Bhutan, exposure to UV rays is a significant concern. Prolonged UV exposure can degrade certain materials, leading to brittleness and eventual failure. Ocean HDPE – 750 Micron incorporates UV stabilizers that protect the liner from degradation, ensuring longevity and reduced maintenance costs.
4. Environmentally Friendly: Ocean HDPE is also eco-friendly, as it doesn’t leach harmful chemicals into the soil or water, preserving the natural environment surrounding the hatchery. This aligns with Bhutan’s commitment to sustainability and environmental preservation, making it an ideal solution for this project.
The Installation Process
Our team of experts oversaw the entire installation process to ensure precision and efficiency. Installing geosynthetic liners is a complex task that requires careful planning and execution to prevent any leakage or gaps in coverage.
1. Site Preparation: Before installing the Ocean HDPE – 750 Micron liner, the site was thoroughly cleared of any debris, sharp objects, or other potential hazards that could puncture the liner. The area was leveled to ensure an even installation and proper water flow within the hatchery system.
2. Liner Deployment: Given the size of the project, deploying 7500 square meters of the liner required meticulous planning. The liner sheets were carefully unrolled and positioned to cover the entire hatchery base. Special attention was paid to overlap between sheets to ensure a watertight seal.
3. Sealing and Testing: One of the most crucial steps in the installation process was sealing the liner at the seams. Our team employed advanced welding techniques to join the Ocean HDPE sheets, creating a seamless, leak-proof barrier. After installation, the liner was subjected to rigorous testing, including pressure and water tests, to ensure the hatchery’s long-term reliability.
Unique Challenges in Crawfish Hatchery Projects
While many companies focus on the product’s benefits, fewer emphasize the challenges unique to hatchery projects. In the Bhutan Crawfish Hatchery project, factors like Bhutan’s diverse topography, the need for rapid project execution, and the seasonal weather posed challenges. Here are some often-overlooked aspects:
1. Adapting to Local Terrain: The mountainous terrain in Bhutan presented a challenge in terms of site accessibility and liner installation. Our team ensured the liner was adapted to the terrain, utilizing flexible installation techniques to maintain the structural integrity of the hatchery despite uneven ground conditions.
2. Temperature Variations: Bhutan experiences varied climatic conditions, from hot summers to cold winters. HDPE materials are known to contract and expand under temperature changes, but Ocean HDPE – 750 Micron’s high flexibility allowed it to perform well under these conditions, maintaining its durability and preventing cracks or tears.
3. Environmental Impact: Crawfish hatcheries have a direct interaction with local ecosystems, and controlling contamination from hatchery waste is critical. Ocean HDPE’s impermeability ensured that no contaminants seeped into the surrounding environment, maintaining ecological balance.
Project Outcomes
The successful installation of the Ocean HDPE – 750 Micron liner has had a significant impact on the crawfish hatchery. The liner’s reliability and performance have helped maintain optimal water conditions, contributing to a healthier, more productive crawfish breeding environment. Furthermore, the project stands as a testament to the high standards of quality, precision, and environmental consciousness upheld by Ocean Non Wovens.
Why Choose Ocean Non Wovens for Your Next Project?
At Ocean Non Wovens, we pride ourselves on delivering geosynthetic solutions that stand the test of time. Our commitment to innovation, quality, and sustainability sets us apart in the geosynthetics industry. Whether you’re looking to build an aquaculture facility, manage water containment, or protect land from erosion, we provide customized solutions tailored to your project’s unique needs.
With a proven track record of success in challenging environments like Bhutan, our products are designed for longevity and efficiency. Partner with Ocean Non Wovens, and experience the difference that premium geosynthetics can make for your next construction project.
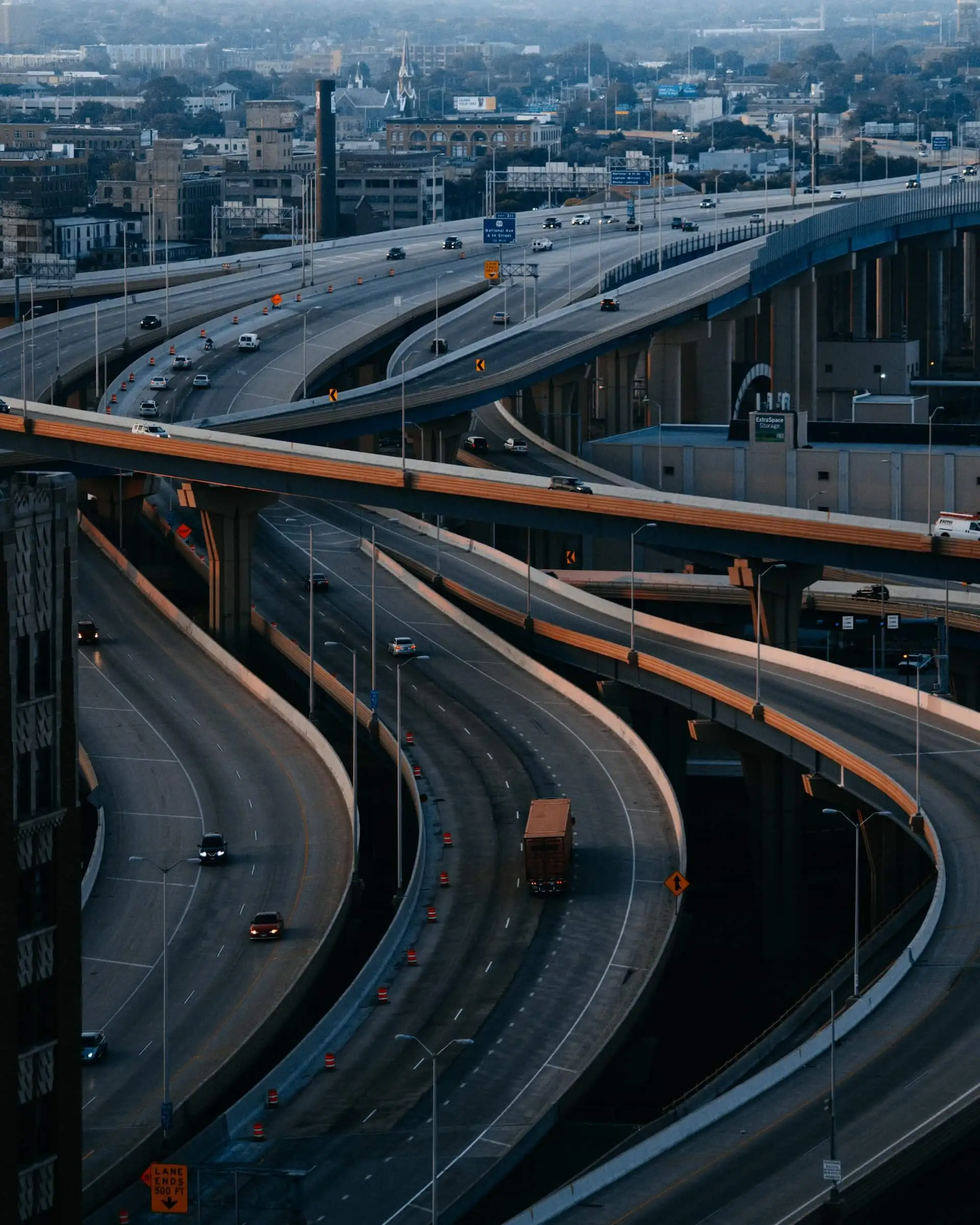